Sugarcane 101: Project Catalyst field trip
Bill Dennison ·Before my workshop and field trip with Project Catalyst, I had not heard of the following terms "dunder, mill mud, billets, ratoons, plant cane, shielded sprayers, cane grubs, controlled traffic, EM mapping, auger delivery, wavy discs, skip row planting, cane stool, bed renovation, cane cockies" and could not even have made an educated guess as to their meaning. There were other terms that I could at least guess a meaning, but did not fully understand like "variable rate application, crop cycle, pivot spray irrigation, molasses, paddock field trials, primary tillage, variable row spacing, green trash blanketing, drip line emitters, air bag boom, precision agriculture". I was also naive as to the process of growing cane from small vegetative shoots, harvesting successive crops, obtaining sugar from cane, the production of molasses, distillation to form the biofuel ethanol, and the fate of sugar mill byproducts. As result of my great Project Catalyst tutors, especially Rob Sluggett, I now have a working knowledge of the sugarcane industry.
So why would a marine biologist from the corn belt of the U.S. spend his time in central Queensland enrolled in 'Sugarcane 101'? The most important reason is to gain an understanding of a significant source of nutrients, pesticides and sediments to the Great Barrier Reef. Another reason is to work with people interested in developing solutions, not just bemoaning the problems. Finally, my experience with science communication and environmental reporting meant that I had something to contribute to Project Catalyst, and they were a receptive group to creating innovative reporting mechanisms.
My first lesson in 'Sugarcane 101' was that cane is not planted, grown, and harvested annually to replant in the following year. Sugarcane is a grass that you mow for several years before replanting. The first crop is called 'plant cane', and each harvest is a 'ratoon'; first ratoon, second ratoon, etc. There is a declining yield in successive ratoons, but considerable cost in replanting (fertilsers, pesticides, fuel and labour), so the cane growers balance yield decline with replanting costs. In the Mackay region, they typically get to about the fourth ratoon before replanting. Replanting is done with shoot pieces of cane (billets).
My next lesson was the sugar mill process. Cane sugar breaks down quickly following harvest, so rapid transport to the sugar mill is crucial. Canegrowers measure their production in tonnes of cane harvested, but the mill pays them in tonnes of sugar delivered. The sugar mills are only open for half a year during harvest. The mills squeeze the sugar out of cane and the remaining fiber, sometimes called bagasse is used to produce biofuel (ethanol). The byproducts of sugar mills include mill mud and dunder which can be returned to the fields, often with nutrient augmentation. Sugar mills not only produce sugar, but also molasses and ethanol.
I had a lesson in the technology and science supporting cane growing. Precision agriculture is about knowing exactly how much and what kind of nutrients and chemicals to apply to different parts of sugarcane fields. The delivery of precise nutrient amounts and ratios to different portions of the field can be achieved using detailed and integrated maps of soil types, field elevations and crop yield which determine optimal fertilizer application rates. Soil maps are obtained by surveying for electromagnetic conductivity and sampling for soil types. Precise field elevations are obtained using satellite remote sensing with fixed base stations. Crop yield maps are obtained from harvester sensors. Multiple layer map integration is used to produce fertilization maps which can be uploaded to global positioning systems used to direct farm equipment and deliver precise fertilizer amounts to different portions of the sugarcane fields. The maps on the global positioning systems can be loaded to the farm equipment from the scientists that have developed the integrated mapping via mobile phone links.
Another lesson that I had was in 'controlled traffic' using global positioning systems (GPS). The GPS allowed for much more than straight lines in farm fields. It meant that the row spacing could be set to conform with farm equipment wheel bases so that the equipment left the center of rows intact and avoided soil compaction. This allowed for nutrients and chemicals to be applied directly to crop roots and reduce loss through runoff. It also even allowed some equipment to be driven in reverse on alternate runs down the field, eliminating the need to swing the gear around at the end of each row.
I also learned that there are substantial differences in approaches to growing sugarcane in dry regions versus wetter areas. The Burdekin River delta is very dry and flat, so cane growers use irrigation, and since the irrigation water is delivered by flowing down the shallow sloping spaces between can rows, they keep the inter row spaces cleared by burning the cane off rather than using green trash blanketing. Green trash blanketing is where the bits of cane not used for sugar extraction like leaves are tossed directly back onto the field during harvesting. This green carpet helps retain water, nutrients and soil while reducing weeds. Billets can be planted through the green trash using sharp discs.
About the author
Bill Dennison
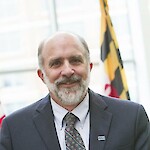
Dr. Bill Dennison is a Professor of Marine Science and Vice President for Science Application at the University of Maryland Center for Environmental Science.